Artificial intelligence and generative AI may be the new technologies on everyone’s lips, with capabilities set to reshape our future. But, while the spotlight shines heavily on these digital advancements, another form of technology is quietly ticking along: 3D printing. This innovation is pushing boundaries in fields like aerospace, medicine, and now watchmaking, and it’s set to go out of this world, quite literally.
Despite rarely being used in the industry, 3D printing and watchmaking do go hand-in-hand. The craft requires precision, patience and pieces – all of which 3D printing is capable of providing with exceptional quality. This is why luxury US-based watchmaker Barrelhand, is using this unique process to produce the Monolith, a high-quality timepiece that not only stands the test of time but also, works perfectly in space.
‘We view space exploration as the next great frontier,’ Barrelhand founder, Karel Bachand tells The Ethicalist. ‘And we are developing innovative tools to meet the challenges of this unforgiving, largely unexplored environment.’
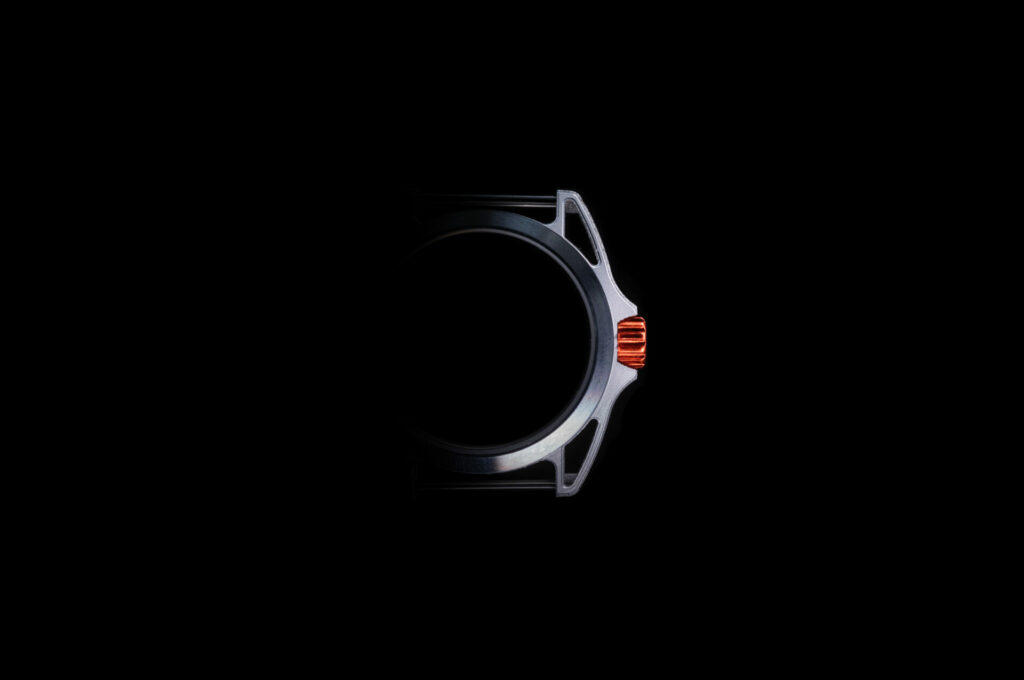
The Monolith 3D printed timepieces have undergone rigorous testing to demonstrate their ability to remain 100 percent accurate even in extreme environments. Barrelhand has referenced NASA’s original extravehicular activity (EVA) guidelines from the Apollo missions to such end. These trials expose the watches to extreme temperatures, vacuum pressure, intense vibrations, and high G-forces, ensuring they can withstand even the harshest conditions that astronauts may encounter.
They have passed these tests via various means, including the design of an air core insulated chassis – so that extreme temperatures don’t dramatically affect oils in the engine, allowing the timepieces to operate for far longer periods of time in space than a traditional watch. Additionally, Karel says, they’ve paid particular attention to the lume, the luminescent material applied to the watch’s components.
‘Our watches are also designed to be ultralight, as the cost per kilogram to send it to the International Space Station (ISS) is nearly $20,000, so every gram that can be saved is critical.’
‘We’ve developed a ceramic lume composite dial that is extremely stable, allowing the display to be as legible as possible even in lowlight settings. Our watches are also designed to be ultralight, as the cost per kilogram to send it to the International Space Station (ISS) is nearly $20,000, so every gram that can be saved is critical.’
To showcase the advanced capabilities of 3D printing, Bachand aims to print not only watch cases in steel and titanium but also the entire movement bridges – the internal mechanism that powers and regulates the timekeeping.
Interstellar Timekeeping
There are however, plenty of things to consider when creating a watch fit for space, such as servicing and repairs, crucial as they hurtle towards other planets. Luckily, 3D printing allows the brand to digitally upload and print replacement parts on Earth or in space.
Pieces can be printed in as little as ten minutes too, such as the Monolith chassis prototype in engineering plastic, using Digital Light Synthesis Process – a rapid 3D-printing process that uses digital light projection, oxygen permeable optics, and programmable liquid resins to produce parts. Printing a batch of 20 chassis in stainless steel or titanium usually takes longer however, at around 20 hours.
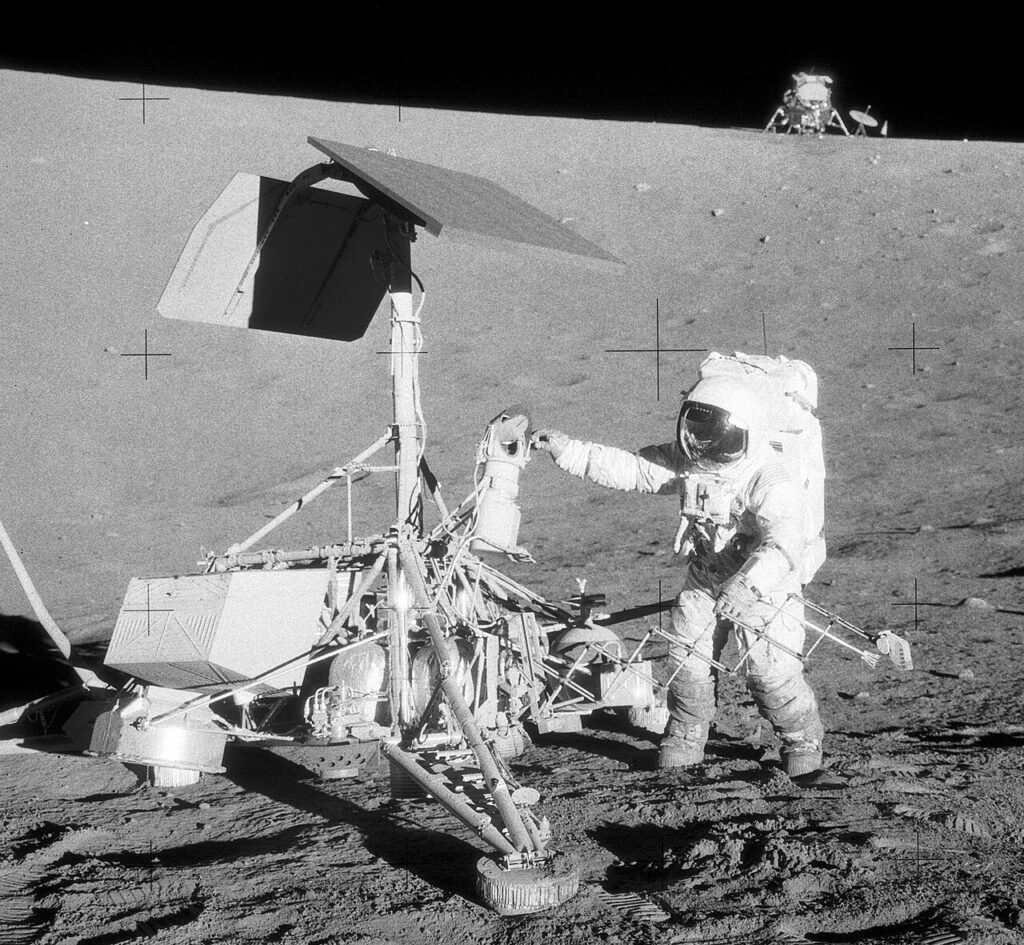
Each and every component of the watches are co-developed by experts in the aerospace and watchmaking industry.
The glass is specially made by a laboratory optics supplier to meet the impact resistance requirements on the International Space Station. For the dial, the brand partnered with RC-Tritec – the developers of the illuminous Super-LumiNova timepiece – to create a ceramic lume which can withstand space temperatures.
‘In total we work with almost 12 different manufacturing experts, and the final assembly is done in the USA by master watchmakers to ensure they are precisely regulated and meet all the testing requirements,’ says Bachand.
From Passion to 3D Precision
Bachand, a mechanical engineering graduate, discovered his passion for watchmaking after watching one of Swiss watchmaker Urwerk’s CGI videos on YouTube. Unable to purchase one of their pieces, Bachand embarked on a project to create a fully functional 3D printed version of the Urwerk’s innovative UR-202, the world’s first fluid dynamics-regulated winding rate watch.
Two years later, his achievement caught the attention of the Urwerk team, who invited him for a meeting. Inspired by this, Bachand founded his own company, leading to the creation of two timepieces: the Project One, which sold out rapidly, and the much anticpated Monolith, priced at $8,750.
Project One served as a research platform to build out the infrastructure and test new technologies like metal 3D printing. Now, Monolith is taking all the learnings and tech from Project One and applying them towards a real-world application.
The brand’s design philosophy is purpose-driven as a tool for the next chapter of space exploration. 3D printing along with lessons from past missions, failures, and new requirements is allowing Barrelhand to build something special from the ground up, with the goal being for its Monolith to operate on longer missions to other planets.
‘We have many exciting missions this year for testing, getting us one step closer to establishing Monolith as the next gen tool for the moon, Mars, and beyond,’ says Bachand.
‘There is still so much room for new advancements and technologies to play a part in the watch industry. This next chapter of space exploration will be extremely challenging and we are excited to grow and develop new tools with it.’