If environmentalism had to nominate its villain, it would likely to be a close run between oil and plastic. Plastic, we’re told, must go, even though many of the products we think of as essential – from computers to car and aircraft parts, our phones to, yes, those solar panels – wouldn’t be possible without it. Even 60 per cent of all clothing material is made from plastics.
And yet plastics – made from petrochemicals, and expected to use up a fifth of all oil production by 2050 – now account for 15 per cent of the global carbon budget, according to the United Nations. It’s success has been the root of its perceived failure: one of its greatest qualities – its long-lastingness – is its greatest downside. It lasts without breaking down for centuries; incinerate it and it releases toxic gases.
‘It’s the mis-use of plastic that is the problem, and a lack of innovation to provide a true alternative.’
‘The fact is that plastic is a brilliant material for certain uses – it’s cheap, lightweight, durable, can be moulded and made colourful, and so on,’ as Heather Carley, head of marketing at biotech start-up Shellworks, explains. ‘It’s the mis-use of plastic that is the problem, and a lack of innovation to provide a true alternative.’
Can Plastic be Fantastic?
The ideal order of events may be to eliminate as much plastic use as possible; then to find ways to recycle the plastic that’s already in circulation; and then, for when new plastics are absolutely needed, to develop ecologically-sound varieties.
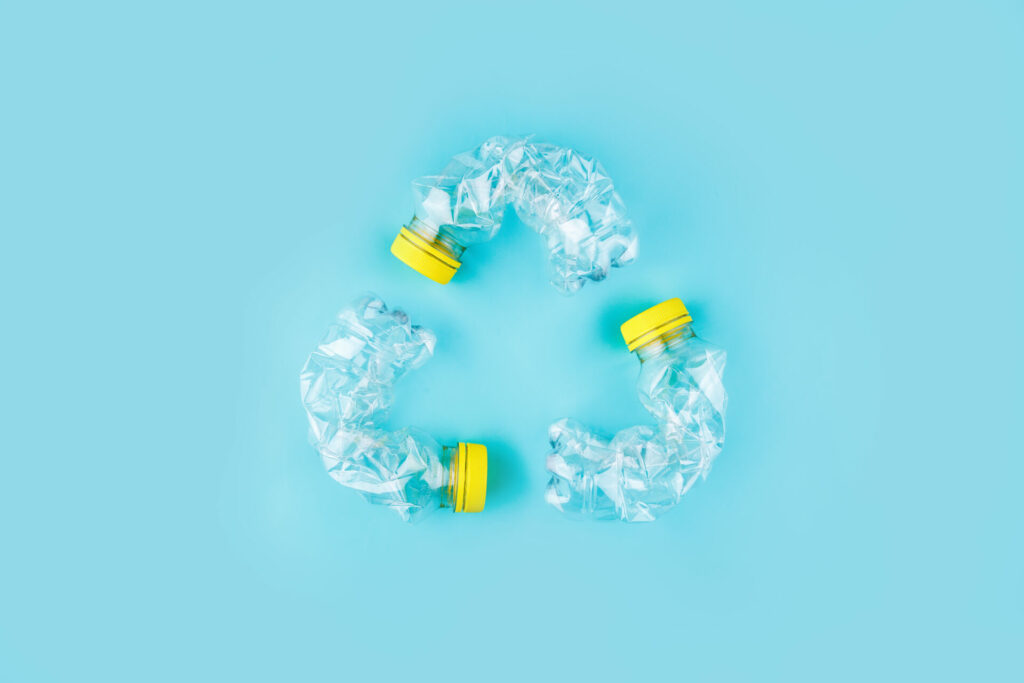
Towards the first step there’s a growing re-purposing or re-introduction of fully recyclable materials that, across different cultures, had widespread use before those ever so-useful plastics came to prominence. Paper pulp, for example, has been used again to make bottles trialled by Coca-Cola – albeit bottles with a plastic lid and a lining made from polyethylene terephthalate, better known as PET. Plastic-replacing uses have also been found for materials the likes of bamboo, hemp and milk proteins, and by re-booting our historically more widespread use of stainless steel or glass.
The danger here is that in our rush to replace plastics with other, already established materials, we lose sight of the big picture: paper bags have a much higher carbon footprint than conventional plastic shopping bags
The danger here is that in our rush to replace plastics with other, already established materials, we lose sight of the big picture: for instance, paper bags and compostable plastic bags, multiple studies have shown, have a much higher carbon footprint than conventional plastic shopping bags; the manufacturing of these turns out to be three times less energy intensive. Similar is true of paper straws relative to plastic ones. It’s this complexity that makes the introduction of some kind of global plastic pollution treaty especially difficult, even as trade tariffs typically make it cheaper to just keep on using plastics.
‘And that’s problematic not least because as consumers we think about plastic but often don’t grasp its full impact on the environment, or we rely on the idea that we’re recycling – we ‘tick that box’ by putting our bottles in the right bin – when only around 9 per cent of plastic is recycled,’ argues Margaux Deguerre, head of marketing at materials science start-up Notpla. ‘If we took into account all of plastic’s negative externalities it would be 10 times more expensive than it is.’
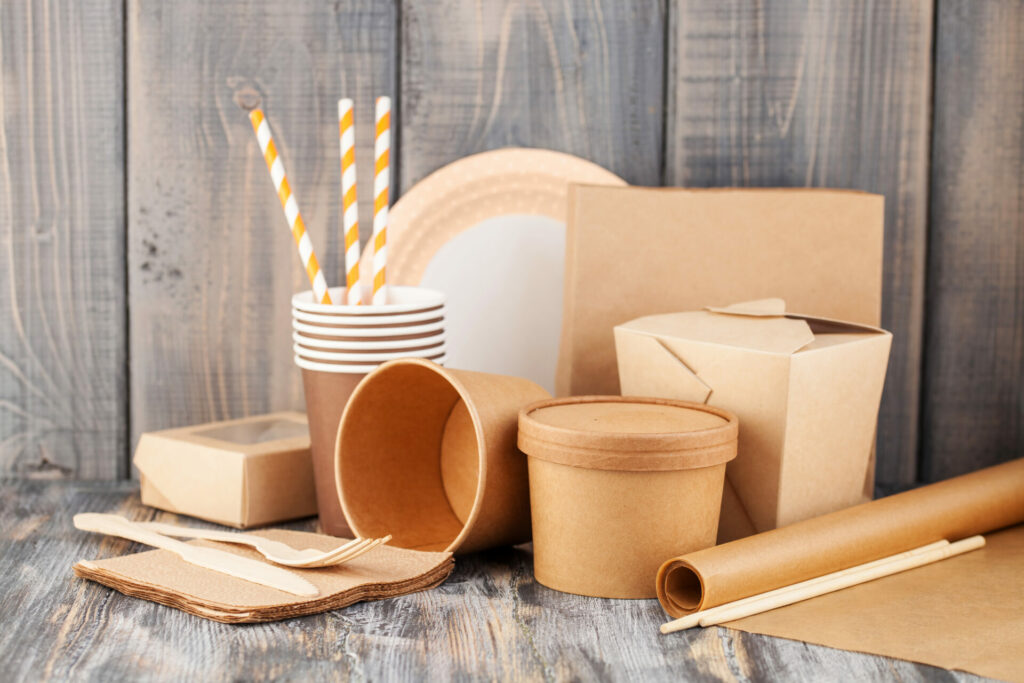
The big picture likewise requires consideration with regards to innovative attempts at upgrading and replacing our eco-damaging plastics with new, eco-friendly equivalents able to provide the same utility, notably through the development from natural sources of so-called bio-plastics or bio-polymers — made from renewable sources the likes of starches, plants and sugars. Some provide benefits but also their own problems.
Polylactic acid, or PLA, for instance, is a popular bioplastic made from corn and often used for single-use items the likes of bottles, packaging and straws. But to then biodegrade it requires super-heating at special facilities. So invariably a lot of it isn’t recycled, or gets shipped out of sight and out of mind – at some carbon cost – to processing plants abroad, where the processing might not actually happen (almost two thirds of all plastic waste ends up in landfill). Then PLA takes almost as long to degrade as traditional plastic.
Bio-Plastic Solutions
More positively, there’s also the bio-plastic polyhydroxyalkanoates – or PHA. This is completely compostable, such that a single-use straw made of PHA takes 90 days to degrade in soil, relative to 200 years for a traditional plastic straw, which might well break down into micro-plastics that enter the food chain.
PHA polymer is also heavier than standard plastic – meaning it sinks and, on the sea-bed, is likely to degrade faster still. And, since not using sustainable feedstocks would be self-defeating, it can be made from food waste or agricultural by-products, as the start-ups Full Cycle and Genecis are pioneering. PHA has already been turned in tableware by a company called OMAO and, by blending PHA with minerals and wood flour, into a single-use forks by Refork.
Expect to see more PHA day to day. And, since this is a boom market driven by hungry new bio-tech companies, expect further original ideas to come along too: the Dutch bio-plastics company Avantium, for example, has created what it says is a completely recyclable plastic using agricultural waste and a compound called mono-ethylene glycol, or MEG, which can be used to make bottles. It’s already struck a deal with Carlsberg and is now building its first factory with plans to start production next year.
There’s also an increased use of what’s known as liquid wood, a strong, mouldable, non-toxic composite material made from lignin, a renewable by-product of paper manufacturing, that’s already being used to make golf tees, toys and speaker cases.
‘The reality is that you can create the best alternative [to traditional plastics] but if it requires, say, a huge change of industry or consumer behaviour, then it’s very tricky.
Certainly the sea looks to be a place of inspiration. Notpla is making plastic replacements – notably compostable condiment sachets and a coating for cardboard takeaway boxes – from fast-growing, carbon sequestering seaweed. Meanwhile Shellworks has created a plastic made from a kind of fat extracted from marine and soil microbes, and which becomes food for bacteria again at the end of the product’s life. Its current focus is on replacing the plastics used in skincare packaging.
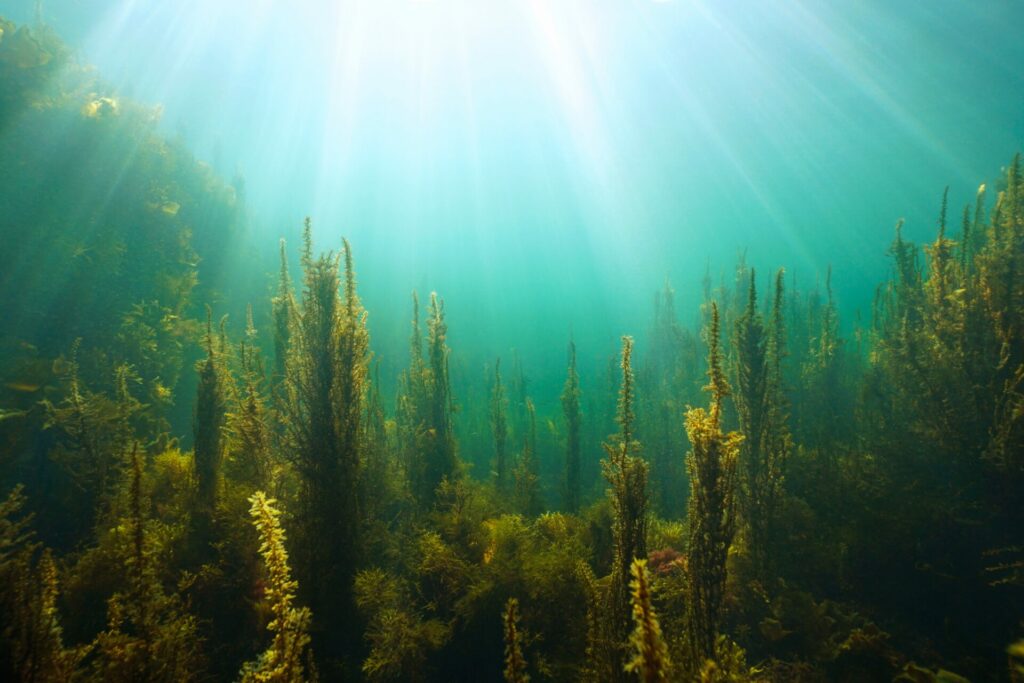
‘The beauty industry brings its own challenges too, because it doesn’t want to sacrifice the aesthetics of its products – since aesthetics is what it’s all about – so it’s not enough to just think about the sustainability and useability of plastic alternatives. You have to think about the way they look too,’ argues Carley. ‘The reality is that you can create the best alternative [to traditional plastics] but if it requires, say, a huge change of industry or consumer behaviour, then it’s very tricky. So there’s a lot of questions to ask right at the development stage of bio-plastics if you want to have a tangible impact.’
The plastics used for packaging of fruit and vegetables may come to be replaced by a tasteless and edible plant-based spray that coats fruit or veg to create a barrier that traps moisture in and keeps air out extending shelf-life.
It’s not just the advent of bio-plastics that is driving this impact and providing functional alternatives to traditional plastics either. Foamed plastic, for example – often used to line attics and roofs for better insulation – can now be replaced by a new material called stone wool, created by melting together slag (a byproduct of steel-making) and natural igneous rock and spun into fibres. The plastics used in flame retardant, acoustic insulation and polystyrene packaging can be replaced by materials made from mycelium, an easily-grown fungi derivative.
Likewise, the plastics used for the packaging of fruit and vegetables – one of the most egregious single uses of plastic but, retailers say, demanded by us consumers – may come to be replaced by a product developed by another start-up called Apeel. It has come up with a tasteless and edible plant-based spray that coats the fruit or veg to create a barrier that traps moisture in and keeps air out, thus extending shelf-life.
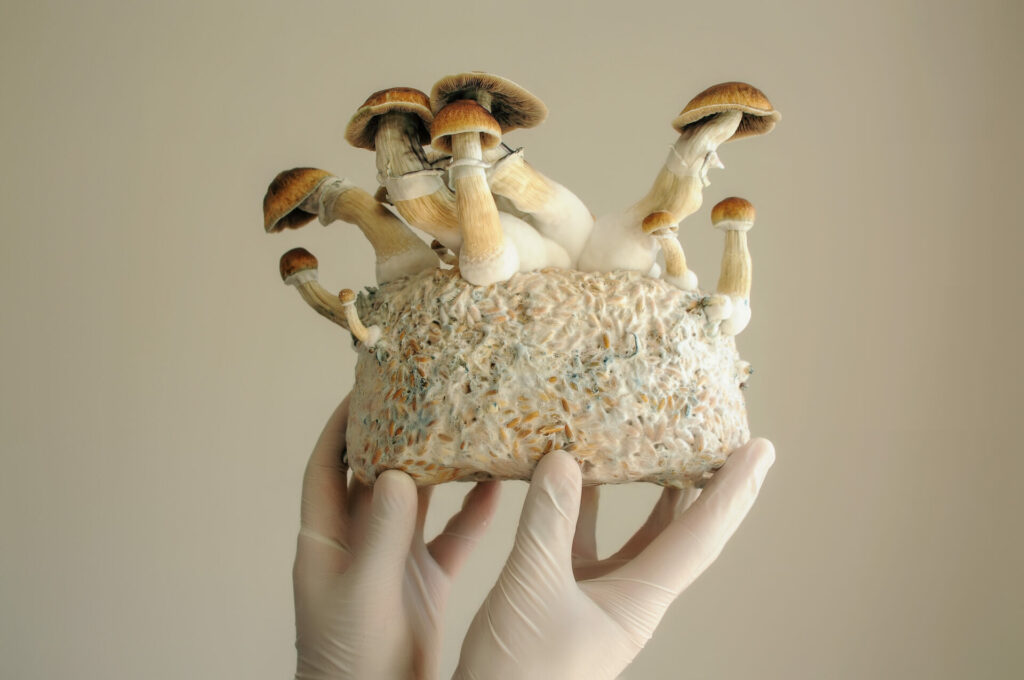
But where are all these amazing ideas in action? Deguerre concedes that it’s one thing to develop these products at the laboratory scale and quite another at an industrial scale. And then encouraging their adoption is a slow, costly process requiring big investment, though that Apeel is now valued at US$2bn speaks perhaps to the enthusiasm for tackling the plastics problem and the potentially huge business opportunity in doing so too.
There’s even a technology being developed that can turn water and CO2 into precursors for certain plastics, hinting at a future where CO2 emitted from plastics could be captured and turned into new plastics.
Yet innovation, thankfully, does look set to provide real solutions: incredibly, there’s even a technology being developed at Rutgers University and its spin-off company RenewCO2 that, it says, can turn water and CO2 into precursors for certain plastics, notably those that could replace PET and polyester fibre. That hints at a future in which the CO2 emitted from plastics as they break down could be captured and turned into new plastics.
The proof, as it were, will all be in the using. Do these new products match the functionality of the wonder material that is plastic as we have known it, and then often blithely discarded it? As Carley puts it, ‘it would be helpful if we could just shift the consumer mindset away from the consumption of plastic but, given how useful it is, that’s just not realistic. Not, at least, until we can offer serious alternatives. And that is happening now.’